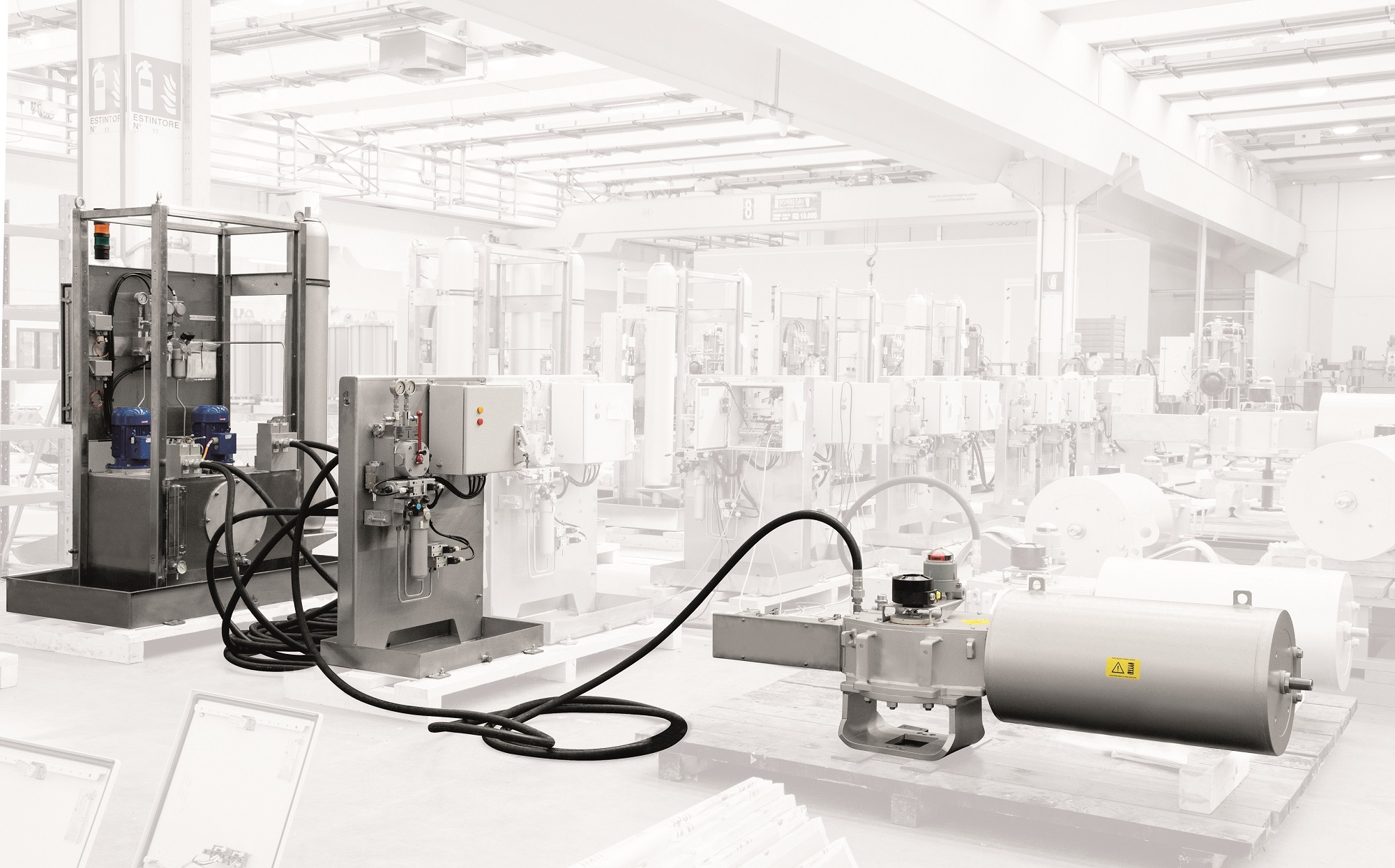
Project: Budowa Blokow, a new ultra-supercritical coal-fired power plant
Location: Opole, south-western Poland
End user: PGE Gornictwo i Energetyka Konwencjonal S.A.
EPC Contractors: ALSTOM POWER
This project concerns units 5 and 6 for a new ultra-supercritical (USC) coal-fired power plant in Opole. Once operational, it will be Poland’s largest coal-fuelled facility, supplying electricity to the equivalent of two million homes. Unit 5 is due
to enter commercial operation in 2018 and unit 6 in 2019. The use of ultra-supercritical technology, which allows producing higher electrical output while burning less coal, will enable PGE to reduce its environmental impact
and meet regulatory requirements. This is particularly important in Poland, where around 90% of fuel for electricity generation is coal or lignite.
The hydraulic unit in the low pressure bleed system controls the steam in the turbine circuit. This application requires high performance and precision. It is composed of three different elements: a quarter turn actuator fitted to a
butterfly valve, a control cabinet and an hydraulic power unit. Due to limited space, all of these components needed to be installed in three different locations.
IMI STI delivered actuators from its RTQH series as well as control cabinets with SmarTrak® controllers. The RTQH series is a range of high torque hydraulic quarter turn actuators with materials selected to withstand the most hostile environmental conditions. With a high speed control it can close the valve within the required two seconds and additionally provides ESD functionality. The actuator is controlled by a SmarTrak positioner, a controller used as a positioning system for proportionally-driven hydraulic actuators with up to two independent channels. It can manage two fully independent actuators. The hydraulic power unit has a special redundant system for both electric motors and pumps. Any alarm condition which is generated on this HPU (eg, low pressure, low oil level, high oil temperature,
motor temperature etc.) is sent to the DCS that can then lock the actuator in position by sending a signal to a solenoid valve mounted on a control panel on the actuator itself.