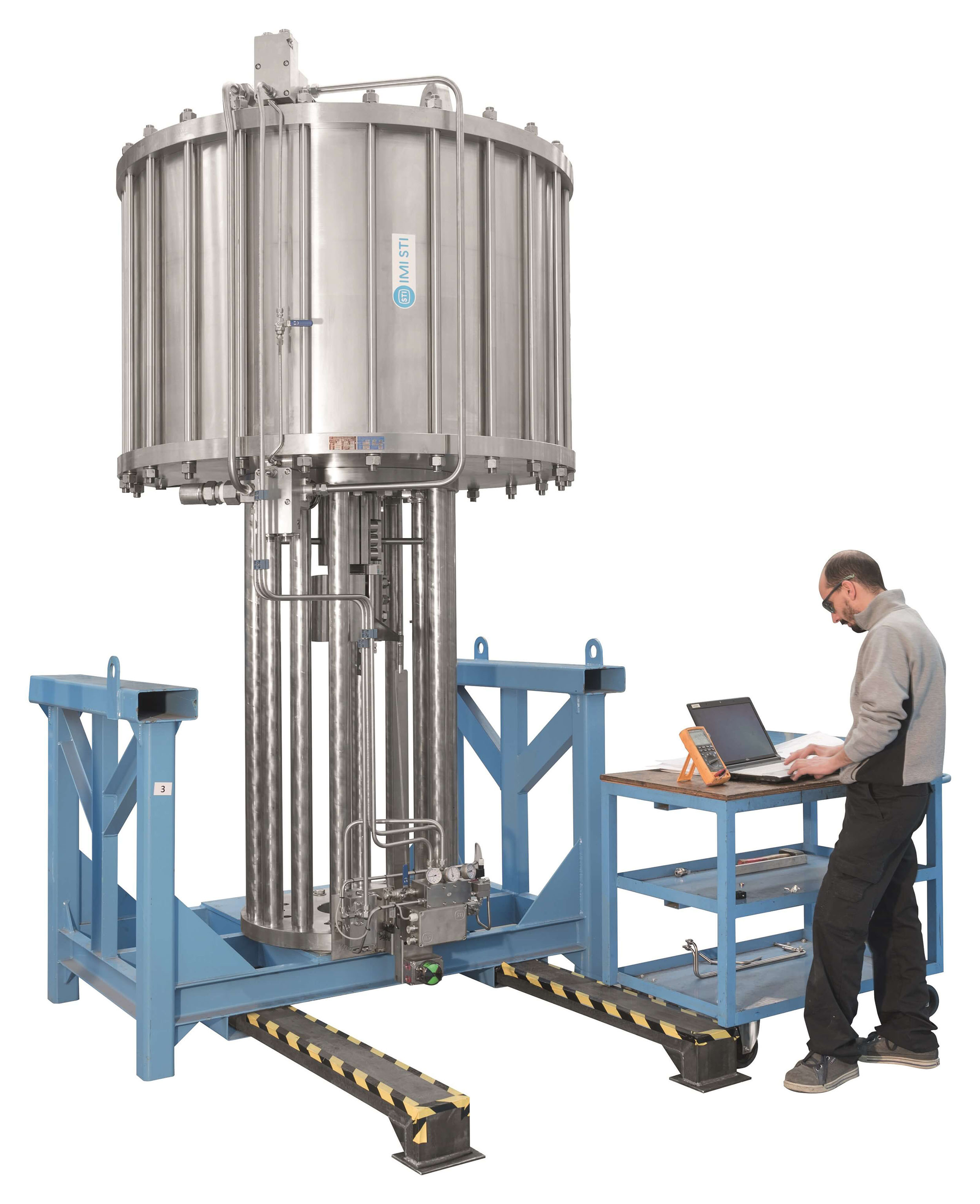
Location: Hammerfest, Norway
End user: Statoil
Project description
To operate the 36’’ gate valve on a Hammerfest LNG plant on the North Sea, Statoil originally had an electrical actuator with about 20 minutes’ stroking time. This actuator had an on/off function.
In case of a tripping request, Hammerfest LNG had to send to flare the whole content in the line and then repressurize the line and the slugcatcher. This was the main, but not the only reason, why Statoil decided to find a new solution. Other requirements included:
- contribute to factory and company goals in reducing the total CO2 footprint;
- have a control function on the valve which could allow someone to operate it under pressure and rapidly deliver feed gas to the turbine after trip;
- the possibility to start the plant within 24 hours after a trip;
- the capability of avoiding the content of the line to flare (more or less 800 to 1.000 ton CO2 each trip) and saving money (a fine has to be paid for each ton of CO2 released into the atmosphere);
- the capability of avoiding the re-pressurization of the line and the slugcatcher after a trip. This means that it is possible to go directly to ramp 2&3 when the factory restarts after a trip
- save 2 hours of production lost during the procedure.
To reach the above aims and overcome other problems already being experienced (such as corrosion and remote position controllability), Statoil was looking for an actuation system with the following features:
- delivered thrust 1.200.000 N;
- 755 mm stroking adjustability;
- full stainless steel corrosion resistant materials (316 or better);
- adjustable mechanical stop for both end strokes (close/open);
- chance to drive the valve in any intermediate position by remote signal (4-20mA HART);
- full stroking time in less than 60 seconds;
- schematic circuit able to make the valve freezing in position in case of any failure (both signal and air failure);
- special design that allows the replacement of the electric actuator and joint’s existing parts, without valve/valve stem dismantling;
- actuator’s dimensions suitable for available room on existing structure;
- actuator and electrical accessories suitable for hazardous area;
- about timing, the replacement has to be done during a specific time frame and restart the plant without any delay, due to obvious major economic losses.
Options
At an early stage IMI STI proposed two alternatives, both of which were evaluated: the hydraulic and the pneumatic options.
On one hand the hydraulic option would need a local HPU, but in such a case there would be some complications due to the Explosion Proof construction and Stainless Steel material requests. On the other hand, for the pneumatic solution, no additional power source would be necessary as instrument air was already available. For this reason the second option was chosen.
Solution
After an in depth site inspection and measurement, IMI STI developed an actuator with a very big thrust corresponding to 1.236.782 N at 7 bar, able to meet the customer requests. To guarantee this thrust IMI STI had to realize an actuator with a 1500 mm nominal diameter and a 755 mm stroke. Due to the harsh environment, and as requested by the customer, the actuator and accessories are made completely from stainless steel 316 and suitable for low temperatures. The design is fully in compliance with PED normative. The yoke, made of 316 stainless steel, is specifically designed to be jointed to the valve top on site and includes the double independent stroke adjuster devices. Obviously the yoke is sized to withstand, with a safety margin, the actuator’s thrust and weight (more or less 7 tons).
Unlike the original on/off application, the new solution requires a modulating valve. For this reason, on the actuator the smart positioner FasTrak® has to be installed: intrinsically safe, fully stainless steel 316 and branded IMI STI. The challenge to achieve less than 60 seconds’ control stroking time was solved by using two large volume boosters of 1 ½” in size (BW model specifically designed and patented by IMI STI in order to operate with FT positioner). During field tests the minimum stroking time achievable recorded was 40 seconds, staying well within the relevant margin from the original request.
For process logic reasons, complying with user requests, in the case of signal and/or air failure the actuator must remain in position. Thanks to a signal fail freeze option on FasTrak and a lock-up device (for air fail), this feature has been achieved.
Finally, a modular design allowed the last challenge faced to be overcome: mounting on site and joint to the existing stem in the quite tight available space. Operation times also have been fully respected.
The above mentioned actuator, with corresponding technical features, has been successfully installed and tested with the support of IMI STI engineering department.