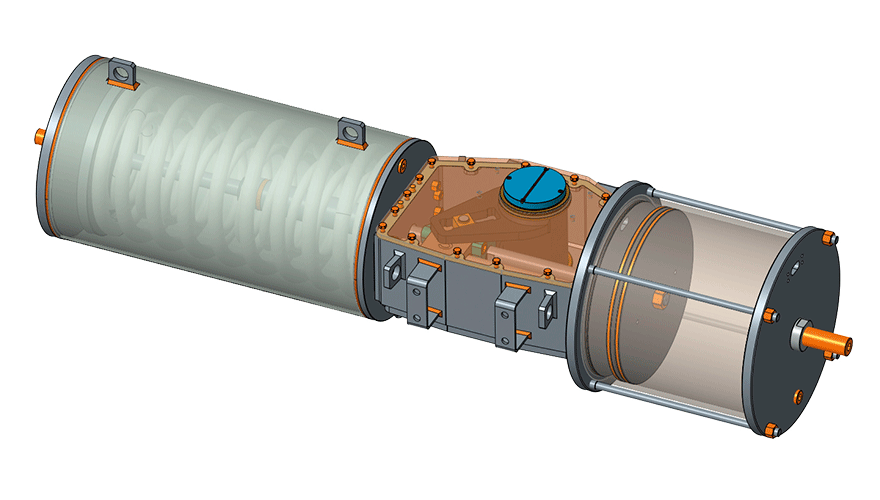
Quarter turn valves have been used for a very long time almost exclusively for on–off regulation. Today, however, they are also used for regulation purposes.
In a number of areas, such as oil & gas, power production, and desalination when the process conditions demand the selection of a quarter turn control valve, the most important and hardest task is to precisely follow the modulating variable position.
This precise modulation capability is in essence dependent on:
- the closed loop local control system composed of the positioner/
controller and the proportional valve (comparable to the nervous system of
a machine); - the actuator (comparable to the skeleton and muscles).
The second of these two parts will be the focus of this article. The majority of pneumatic/hydraulic actuators use scotch yoke technology to transform the linear piston movement into a rotary one. Theoretically, this technology is simple and robust in its application, though the state-of-the-art field application has serious drawbacks. Gaps between the sliding block and the scotch yoke slot inevitably have a negative influence on both the precision and functional dynamics (i.e. hysteresis, dead band, small step response, etc.). This inaccuracy becomes inevitable and persistently increases when then moving on to examine the operative life of the actuator.
The dynamic precision attained in the system, composed of a controller and an actuator, is determined by the component with poorer performance of the modulating chain. A perfect control system matched with a low performance actuator will result in poor positioning control.
IMI STI has been developing control technologies and related products since its inception. Because of this, we understand the increased attention implied by the use of a control actuator when compared to standard on–off applications. While designing the eventual machine, over the correct sizing (which has to follow different rules than the on–off situation), particular attention has to be paid to avoid the increase of dynamic and static friction and to any possible unwanted mobility between different parts. There, therefore, needs to be an element limiting gaps, and wear. While rigidity can be obtained through an appropriate structural design, a more complex question arise to reach both a limited friction and to avoid initial and operative wear gaps/backlash during regulation.
In order to reduce sliding friction within the scotch yoke slot to an acceptable level, the actual solutions at our disposal are:
- the use of a rotary pin in order to transform sliding into a rolling friction;
- interposing a sliding plate with low friction–high mechanical performance, and finished with extremely low roughness and hardened on the sliding surface.
The two main disadvantages of the first solution are clear. To insert the roller and permit it to rotate, means that this object cannot touch both surfaces simultaneously, maintaining a native gap. Moreover, the contact surface between the pin and the scotch yoke is, almost equal to zero. This leads to extreme local pressure, greatly in excess of plastic strain, and as a consequence material deformation, with an increase of the gap.
The second solution shows intrinsically better results because of the increased surface distribution of the force, thus leading to lower deformation and wear (though they are still present). The main disadvantages when compared to the first solution presented are the increased costs and augmented number of pieces, comprised with possible untoward tolerance permutations (non-negligible gaps also with precision machining).
Further to this, IMI STI has developed a technical solution associated with sliding surface technology. This patented technology, resolves the native and the wearing-related gap between the sliding block and the scotch yoke, while maintaining friction values at comparable levels to the state-of-the-art technology.
A load endurance test was carried on in order to validate the new technology and the results have exceeded expectations.
To better understand the differences between the actual and the new technologies, a further load endurance test was carried out on two identical actuators, which differed only in sliding technology.
At the end of the comparison test, the position liability of the standard was shown to be 400% times worse than the new technology.
The working principle is very simple in that it is totally mechanical and auto-adjusting during the operating life of the component. It does not change the size of the detail, so it’s perfectly retroactive. The system comprises a mechanism that is mechanically irreversible, which adapts the dimension of the sliding block to the slot of the scotch yoke, avoiding any gap. The contact between the sliding surfaces remains on the interposed sliding plates. The relative dimensions between the slider and its case, auto-adapting till contact has been made. The contact force applied by the system is several orders of magnitude lower than that generated during field operations, thus leading to virtually zero gaps, and there is no loss of performance due to the increased friction.
The same mechanism allows automatic and continuous adaptations while the actuator is operating, compensating the dimensional variations on pieces with relative movement and relevant contact pressure (i.e. due to surface adjustments, wear, etc.).
Quarter turn valves change do not change their CV linearly on their whole range, concentrating most of the variations in one or few parts of that. This demands a very precise control system in order to reach satisfactory control performances in modulating variable position of the valve.
This new quarter turn regulating actuators technology (called Zero Backlash) for gap avoidance and recovery is available on the whole range with scotch-yoke mechanism.